Heat pressing on a cotton-polyester blend involves a precise understanding of fabric dynamics and a commitment to achieve impeccable results. As an essential tool in custom apparel and textile industries, mastering the nuances of heat pressing on this popular fabric blend demands both expertise and the right techniques.
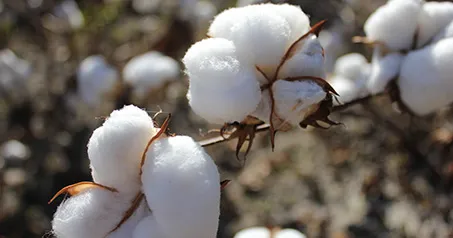
Cotton-polyester blends, typically recognized for their balanced comfort and durability, present unique challenges when exposed to high temperatures. Unlike pure cotton, these blends contain synthetic fibers that react differently under heat. The polyester component can easily scorch or melt if improperly handled, making it crucial to adhere to specific guidelines when applying heat-transferred designs.
For achieving that perfect press on cotton-poly blends, temperature settings are paramount. Experienced professionals often recommend a median temperature range, typically between 270°F and 300°F (132°C and 149°C). Maintaining this range helps in protecting the polyester fibers while ensuring that the adhesive used in transfers or vinyl thoroughly binds with the fabric. Moreover, pressing times are equally critical, generally hovering around 10 to 12 seconds. Adhering to these parameters allows for robust adhesion without compromising the fabric’s integrity.
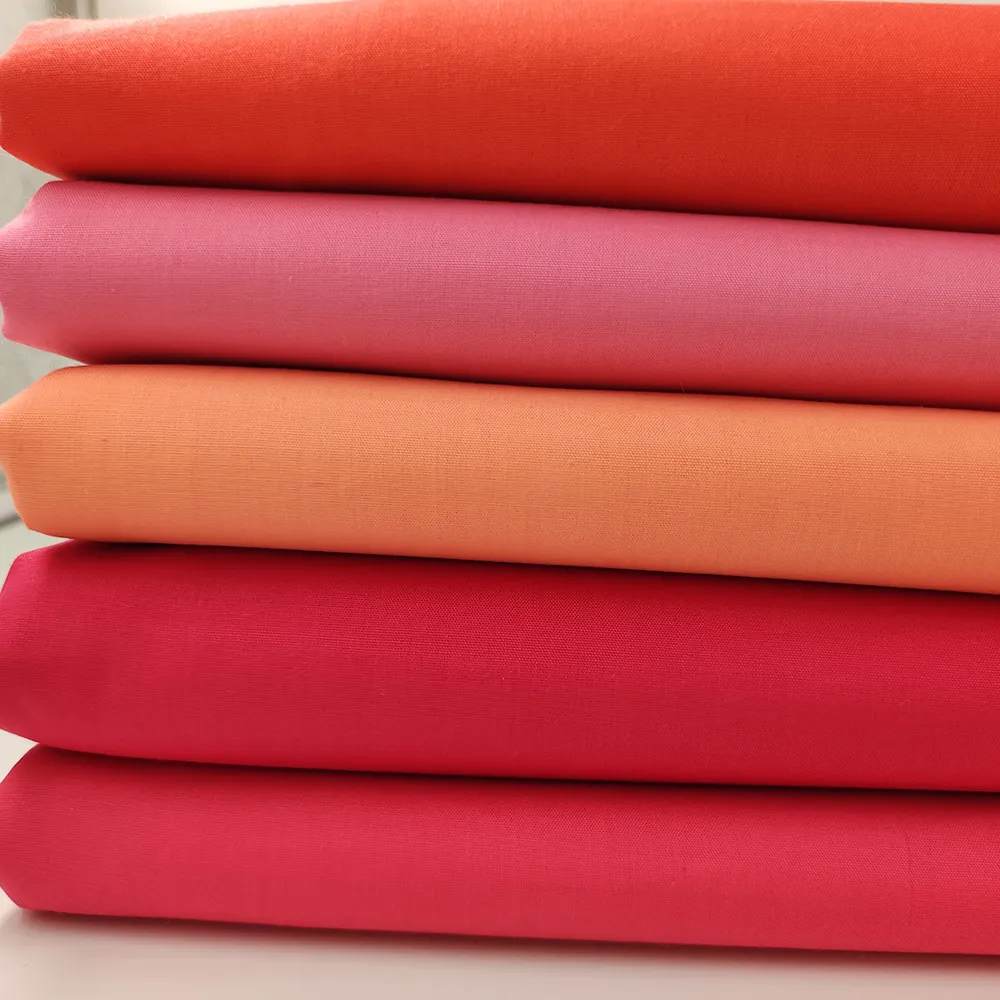
Another vital consideration is the type of heat transfer material used. Experts in fabric customization often select polyurethane-based heat transfer vinyl (HTV) due to its elasticity and compatibility with synthetic fibers. This selection mitigates risks commonly associated with polyester, such as scorching, while providing a seamless blend with the cotton component. Professionals also emphasize pre-pressing the fabric to eliminate moisture and wrinkles, ensuring a smooth and even application surface.
Expertise in heat pressing is also reflected in selecting the right pressure settings. While too much pressure can imprint press marks on sensitive blends, insufficient pressure may result in incomplete transfers. Accordingly, moderate pressure is recommended. Investing in quality heat press machines that allow for precise pressure adjustments can make a significant difference in achieving professional results.
heat press cotton poly blend
Furthermore, it is essential for practitioners to understand the significance of cooling. A popular technique involves allowing the transfer to cool slightly before peeling away the carrier sheet. Known in this realm as the warm peel technique, it stands as a safeguard against potential damage, providing time for the adhesive to set while maintaining the transfer’s fidelity.
Incorporating authoritative sources and hands-on experience, professionals often advise new entrants into the heat pressing world to conduct small-scale tests. A controlled trial on a lesser visible part of the garment can provide insights into how the blend will react to the layered complexities of heat, pressure, and time.
Trustworthiness in the heat pressing domain is built on consistent outcomes and informed practice. Building a repertoire of successful projects not only establishes one’s credibility but also leads to sustainable business growth. Meanwhile, staying abreast of newer technologies, such as advanced heat press machines with programmable settings, ensures adherence to industry standards and best practices.
By understanding these key elements—temperature, timing, material selection, and pressure—those engaging with cotton-poly blends can transition from novice enthusiasts to authoritative figures in the textile design industry. Such mastery not only elevates the quality of personalized garments but also cements a practitioner’s status as a trusted expert in heat pressing.